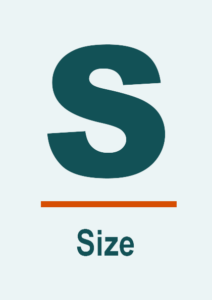
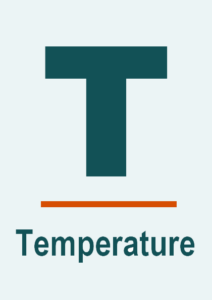
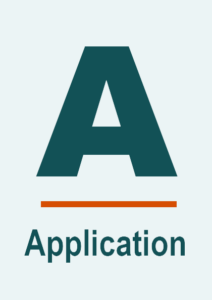
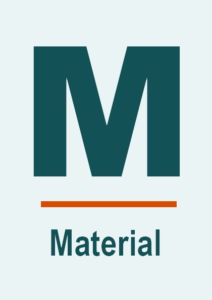
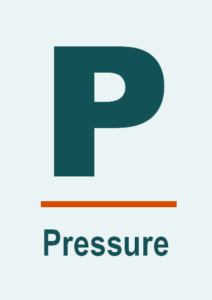
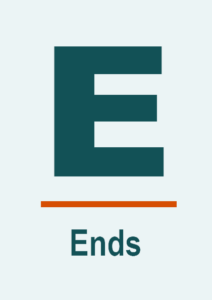

Delivery—covering factors like delivery timeframe, installation requirements, and adherence to industry standards—is an essential consideration in industrial hose selection because it ensures timely deployment, compliance, and operational readiness. Here’s why:
Delivery Timeframe
- Meeting Operational Deadlines: Timely delivery of hoses is critical to avoid disruptions in operations. Delayed deliveries can halt production or maintenance schedules, leading to financial losses.
- Emergency Replacements: In cases of unexpected hose failures, fast delivery ensures minimal downtime and quick restoration of operations.
Installation Requirements
- Ease of Installation: Hoses must arrive with the correct fittings, pre-assembled ends, or ready-to-install configurations to simplify setup and reduce installation time.
- Specialized Tools or Support: Some applications may require specific tools, equipment, or expertise for installation. Factoring this into delivery ensures that everything needed is available when the hose arrives.
Compliance with Standards
- Regulatory Adherence: Certain industries (e.g., food, pharmaceuticals, or aerospace) require hoses that meet specific standards like FDA, ISO, SAE, or other certifications. Ensuring compliance during delivery prevents regulatory issues and guarantees operational safety.
- Industry-Specific Certifications: Hoses intended for hazardous materials, cleanrooms, or high-pressure environments must adhere to strict standards. Verified compliance ensures the hose performs safely under expected conditions.
Operational Compatibility
- Custom Specifications: Delivered hoses must match exact specifications for pressure, temperature, material, and size. Incorrect or mismatched hoses can delay implementation or cause failures.
- Pre-Testing and Documentation: Some deliveries may include pressure tests, chemical compatibility certifications, or other documentation to verify the hose’s suitability for its intended application.
Safety and Reliability
- Regulatory Labeling: Properly labeled hoses with certifications ensure operators can quickly identify and verify compliance, enhancing workplace safety.
- Mitigating Risks: Ensuring hoses meet delivery expectations, including adherence to standards and readiness for installation, minimizes the risk of accidents or system failures.
Cost Efficiency
- Avoiding Project Delays: Delays in delivery or installation due to incorrect specifications or missing components can lead to costly downtime and rescheduling expenses.
- Streamlined Operations: Timely and compliant delivery reduces the need for reordering, additional labor, or emergency purchases, lowering overall costs.
Customer Satisfaction
- Tailored Solutions: Delivering hoses that meet customer-specific requirements ensures satisfaction and builds trust in supply chain reliability.
- Proactive Support: Coordinating delivery with installation and compliance considerations demonstrates a commitment to meeting operational needs efficiently.
In summary, delivery considerations encompass more than just timely arrival—they include compliance, installation readiness, and adherence to industry standards. Overlooking these factors can lead to operational delays, increased costs, and potential compliance violations.