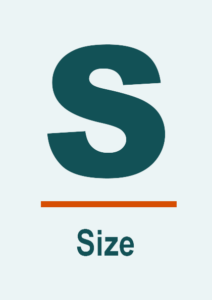
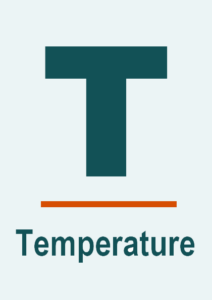
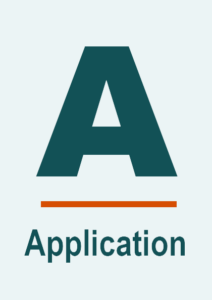
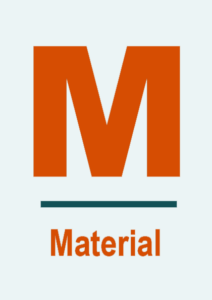
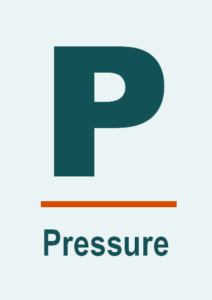
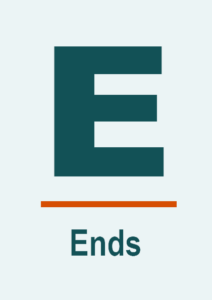
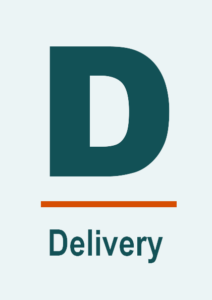
Material of the hose—designed for the type of fluid or material being transported—is crucial for industrial hose selection because it directly impacts the hose’s safety, compatibility, and durability. Here’s why:
Chemical Compatibility
- Resistance to Chemicals: Different fluids, such as acids, bases, oils, or solvents, can degrade certain hose materials. Selecting a chemically compatible hose lining prevents corrosion, swelling, or cracking, ensuring safety and reliability.
- Contamination Prevention: Incompatible materials can leach into or react with the conveyed fluid, contaminating the product. This is particularly critical for food-grade, pharmaceutical, or high-purity applications.
Handling Abrasive Materials
- Abrasion Resistance: For hoses used to transport abrasive materials like slurries, sand, or cement, the inner lining must resist wear to avoid erosion. Improper selection can lead to rapid degradation, leaks, and loss of performance.
- Minimized Wear: Durable materials protect the hose from internal wear, extending its lifespan even in harsh applications.
Gas and Vapor Compatibility
- Permeation Resistance: Some gases can permeate through certain hose materials, reducing efficiency and posing safety hazards. Choosing the correct material ensures containment and minimizes losses.
- Explosion Prevention: Incompatible hose materials with gases can lead to swelling, rupture, or chemical reactions, creating a significant safety risk.
Food-Grade and Clean Applications
- Sanitary Compliance: Food, beverages, or pharmaceuticals require hoses made from materials approved for safe use, such as FDA- or EU-certified compounds. These materials must resist contamination, odors, and staining.
- Easy Cleaning: Materials must tolerate frequent cleaning and sterilization processes without degrading, ensuring product integrity.
Temperature Resistance
- Material Behavior: The selected material must handle the fluid’s temperature range. High temperatures can cause softening, while low temperatures may make the hose brittle, both leading to failures.
- Multi-Material Layers: Some applications may require composite hoses with multiple material layers to handle both temperature and chemical exposure simultaneously.
Operational Safety
- Preventing Failures: Incorrect material selection increases the risk of leaks, ruptures, or hazardous chemical reactions, jeopardizing operational safety and workplace health.
- Pressure Handling: The material’s strength and flexibility must support the operating pressure of the fluid without degrading under stress.
Longevity and Durability
- Resisting External Stressors: In addition to internal compatibility, the outer material must withstand environmental factors like UV rays, moisture, or abrasion, ensuring overall hose durability.
- Minimizing Downtime: Properly selected materials reduce the frequency of replacements and unscheduled maintenance, improving productivity.
Cost Efficiency
- Reduced Replacement Costs: Using the right material minimizes wear, degradation, and contamination, reducing the need for frequent replacements.
- Operational Continuity: Material compatibility prevents interruptions caused by hose failures, ensuring consistent performance and efficiency.
In summary, selecting the appropriate material for the hose ensures chemical compatibility, durability, and safety for the specific fluid or material being transported. Ignoring material requirements can result in failures, contamination, and significant operational and safety risks.