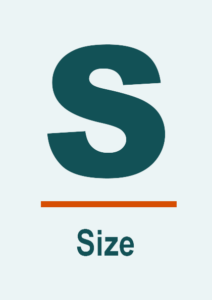
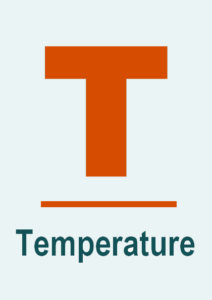
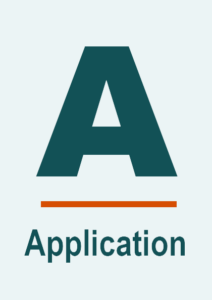
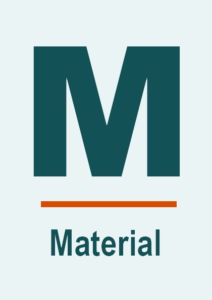
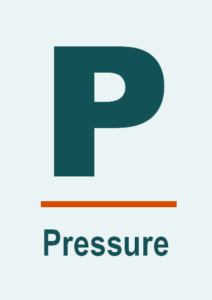
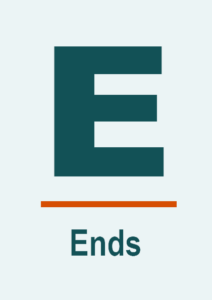
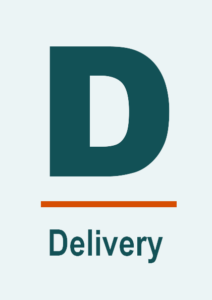
Temperature of the conveyed product and the external environment—are critical for industrial hose selection because they directly influence the safety, performance, and longevity of the hose. Here’s why:
Material Compatibility
- Internal Temperature: Hoses are constructed from specific materials designed to withstand certain temperature ranges. If the product temperature exceeds these limits, the internal lining of the hose can degrade, potentially causing leaks or contamination.
- External Temperature: High external temperatures can compromise the structural integrity of the hose’s outer cover, leading to cracking, hardening, or delamination.
Working Pressure Reduction
- Elevated temperatures reduce the strength and flexibility of hose materials. This lowers the maximum working pressure the hose can safely handle, as noted in the image. Operating a hose beyond this reduced pressure can lead to catastrophic failure, especially in high-pressure systems.
Thermal Expansion and Stress
- Hoses exposed to high temperatures may experience thermal expansion or softening, increasing the risk of kinks or bursts. For hoses conveying cold fluids in hot environments (or vice versa), there may be rapid temperature changes that cause stress on the hose layers.
Operational Safety
- Operating near the upper temperature range of a hose increases the chance of accidents, as materials can lose their elasticity or become brittle. Ensuring proper temperature specifications reduces the risk of failure during critical operations.
Cost Efficiency
- Improper temperature handling results in frequent hose replacements and downtime for maintenance. Selecting a hose suitable for the expected temperature range minimizes wear and maximizes operational efficiency.
In summary, temperature considerations are vital in hose selection to ensure the system’s reliability, safety, and long-term cost-effectiveness. Ignoring these factors can lead to compromised operations, environmental hazards, and equipment damage.